Joining molded plastic parts can be challenging. Adhesives, bolts and solder can only go so far. Ultrasonic welding offers a clean, reliable and strong alternative.
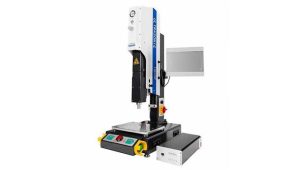
An ultrasonic plastic welder converts electrical energy into mechanical vibrations using piezoelectric crystals. The energy is then regulated by a booster that increases or decreases the amplitude of the vibrations. Read on Ultrasonic Plastic Welding Machines Florida for more details.
Unlike other welding methods, ultrasonic plastic welding is used to join plastic parts without applying any heat. The technology is popular in the automotive industry for a number of reasons, including the precision and quality of the joint it produces. It also offers advantages such as high efficiency, fast cycle times and automation. The technique is also useful in joining thermoplastic components that will be exposed to harsh environmental conditions such as rain, snow or mud.
Ultrasonic welding is best suited for soft, amorphous thermoplastic materials such as polyphenylene oxide (PPO) and acrylonitrile butadiene styrene (ABS). It is generally not feasible to weld semi-crystalline materials like polyvinyl chloride (PVC) or cellulose acetate (CA/B/P) because their higher melting point prevents them from fusing. To ensure a strong bond, it is important to choose an appropriate resin grade and to incorporate fillers when necessary to increase strength or dimensional stability.
A key aspect of successful ultrasonic welding is achieving the correct balance between amplitude, time and pressure. The generator in an ultrasonic welding machine produces high-frequency electricity that is converted to mechanical vibration by the converter and a booster before it is directed to the weld horn. The amplitude of the vibrations determines whether or not the parts are welded together. It is important to ensure the amplitude range is compatible with the materials in use because it is difficult to overcome problems that can result from an out-of-range amplitude.
The amplitude of the vibrations must be sufficiently high to initiate the melting of the plastic in the weld area. This is determined by the ratio of the MFI of the two dissimilar materials in question. The MFI represents the percentage of radicals within each polymer and indicates how easy it is for those radicals to transform from a solid into a liquid state. Two plastics with different MFI values may not fuse successfully, and chemical compatibility can be gauged through a comparison of Tg, melt flow index, and the percentage of free radicals.
One of the most common problems encountered when using an ultrasonic welding machine is non-uniform welds. This is usually a result of poor part cleaning or contamination that can reduce the efficacy of the process. It can also occur if the horn, fixture and part aren’t aligned properly.
Welding Energy
The ultrasonic plastic welding process relies on vibration energy to make a strong and durable bond between two components. This method is a popular choice for manufacturers of products that require a tight seal, such as medical devices and automotive components. Ultrasonic plastic welding also offers a number of advantages over other joining techniques, such as screws and adhesives. It can be performed quickly and is less likely to cause contamination or product failure.
To get the most out of an ultrasonic welding machine, it’s important to understand how the machine works. The heart of an ultrasonic plastic welder is the transducer assembly, which consists of three core parts: the converter, booster, and weld horn. This assembly is usually made of piezoelectric crystals or magnetostrictive materials. The power supply converts standard electrical current into a high-frequency mechanical vibration that is transmitted by the booster and weld horn to the plastic being welded.
The energy from these vibrations is converted to heat by friction between the bonded parts. This heat can be concentrated in a small area, which makes it useful for welding difficult-to-melt plastics. However, it is important to note that this method may not work well with all types of plastics. This is due to the differences in the melting point of different materials.
An ideal material for ultrasonic plastic welding will have a relatively low melting point and a low vapor pressure. The material must also be chemically compatible with the other parts to form a molecular bond. For this reason, the technique is most effective with soft thermoplastics.
The hardness of a plastic is also an important factor to consider. Ultrasonic welding is not suitable for very hard or brittle plastics, such as polycarbonate or polypropylene. Additionally, the thickness of the plastic will also affect the welding performance. Thinner plastics can often be welded using ultrasonic welding, but thicker plastics will need more energy to melt and join together.
Welding Amplitude
Using an acoustic frequency, ultrasonic welding is able to create a strong bond between two plastic pieces. It can also weld different materials together, as long as the parts are compatible. This is because the high-frequency vibrations create a solid joint without melting the plastic. Whether you are assembling medical devices, automotive components or agtech products, ultrasonic plastic welding can help you create durable and reliable bonds that will keep your product secure.
There are several variables in the ultrasonic plastic welding process that need to be taken into consideration to ensure a quality weld. These variables include welding time, welding energy and the welding amplitude.
Welding time is the amount of time, usually in tenths of seconds, that the welder head applies pressure and amplitude to the thermoplastic to weld it. Welding time varies depending on the type of plastic and the application. For example, staking plastic over metal requires longer weld times than near-field welding. The welder head also controls the time when a hold is applied after the ultrasonic vibrations are applied to the plastic. The hold time is generally half the welding time.
The welding amplitude is the strength of the ultrasonic vibrations generated by the welder head. The amplitude is determined by the power of the generator, the size and shape of the parts being welded, and the distance between the weld head and the transducer surface. The higher the amplitude, the more energy is produced by the ultrasonic vibrations. A higher amplitude is required for welding harder, more dense plastics than softer, less dense plastics.
When a welder is triggered, the sound waves travel through the plastic and metal to heat them up at their points of contact. This causes the plastic and metal to fuse together into a solid, hermetic joint. The welding amplitude is important because it determines the intensity of the energy that travels through the joint. A high amplitude produces a stronger weld, while a low amplitude produces a weaker weld. This is why it is important to choose the right welder for your project.
Welding Distance
Ultrasonic plastic welding machines generate vibrations that transmit energy to the interface between two parts. This friction generates heat that melts the parts together, creating a strong bond. The process requires less pressure than traditional welding methods, and the welds produced are clean, mark-free and corrosion-free. It is also a faster, more efficient and more cost-effective method of joining plastics.
When using an ultrasonic welding machine, it is important to carefully consider the power capabilities and frequencies of the welder in order to achieve the desired results for your application. The appropriate frequency will depend on the thickness of the materials being welded. Choosing the right frequency will ensure that your welds are as strong and reliable as possible.
Welding modes offered by the sonic plastic welder are another factor to consider when selecting the best system for your application. These weld modes allow for easy control of the welding process, providing flexibility and precision when adjusting weld parameters. Welding mode settings include weld time, energy and collapse distance control.
One of the most common problems in ultrasonic welding is overwelding, which occurs when more energy than needed is applied to the weld area. This can result in a weak weld that is not strong enough to meet your assembly specifications. An overweld may be caused by a combination of factors, including an insufficient amount of energy being used or welding for too long. In addition, the weld travel distance, or collapse distance, can be too high. This can be corrected by reducing the pressure, trigger force and down speed to reduce the overall energy input. The amplitude of the welder can also be reduced by changing to a lower ratio booster, digitally reducing the amplitude percentage or using amplitude profiling.
In order for an ultrasonic plastic welder to work properly, the parts must be similar in material and thickness. Different thermoplastics have different chemical compatibilities, and they will not be able to form a molecular bond unless their chemical composition is the same. In addition, lubricants and plasticizers can decrease the weld strength of certain materials.